Compact compressors that operate with tip Mach numbers above 0.5 and Reynolds numbers below 100000 are of interest for domestic appliances and small gas turbines.
An axial compressor can be designed to be smaller than an equivalent centrifugal compressor. However, the performance of such a compact axial compression system is limited by increased viscous losses and reduced flow turning caused by operation at low Reynolds number (Re). This research aims to develop an improved understanding of the loss mechanisms at low Re in axial compressors and to explore how these losses can be reduced through design changes.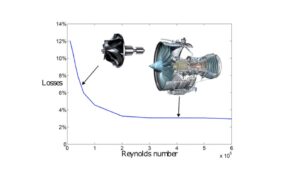
Figure 1: 2D profile loss variation indicating typical Re for a domestic appliance compressor and a jet engine compressor
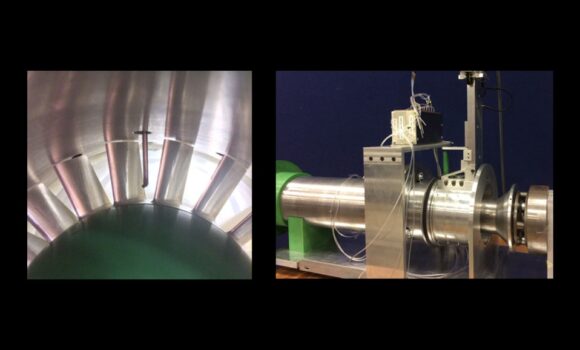
Figure 2: Cascade experiments on low Re aerofoils
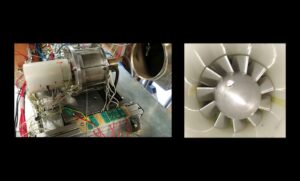
Figure 3: Turbojet driven compact axial compressor rig – (a) Rig Assembly and Instrumentation; (b) View onto Compressor Rotor
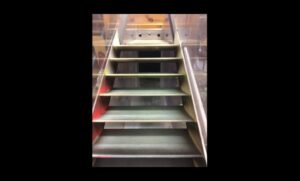
Figure 4: Scaled up low-speed axial compressor rig with miniature 5-hole probe
Cascade experiments using a low speed wind tunnel has been used to investigate the 2D performance of low Re aerofoils, see Fig. 2. The wind tunnel can be run at different flow speeds and the cascade can be rotated through a range of incidence angles. Flow visualisation and wake traverses with a 3-hole probe are used to measure the performance. Figure 3 shows a compact compressor test rig powered by a turbojet engine, running at speeds of up to 120000 rpm. Casing pressure tappings, thermocouples, a thrust sensor and a fuel flow meter are used to measure the compressor performance. Figure 4 shows a 5x scaled-up single stage axial compressor rig. Tests have been conducted across a range of Re of 10000-100000. The flow field can be measured using detailed area traverses with a miniaturised five-hole probe at the rotor inlet, rotor exit, and stator exit. The probe was specifically designed and calibrated for the scale of the experiments and methods to improve the accuracy of the measurements have been applied including a probe geometry correction. The results are being used to understand the compressor loss sources and to explore how the 3D aerodynamics vary with operating point and design features.Associated Team