Overview
Simulating turbomachinery flows using high-fidelity computational methods.
One of the greatest challenges to modern computational fluid dynamics (CFD) is to fully simulate the turbulent flow within an aero engine. Within the engine there are strong interactions of stationary and rotating blades which create a highly unsteady and nonuniform flow field that cannot be simulated correctly with current turbulence models. This is important because unsteadiness and turbulence affects both the aerodynamic efficiency and the heat transfer from the gas to the metal components; the life of the turbine blades is determined by the heat-load which is very sensitive to turbulent convection. Experimental measurements of turbulence properties within the engine are also very difficult to achieve due to the complexities of performing fast-response measurements within engine-scale experimental rigs.
Improving modeling methods is vital for the future design of more efficient aero engines with increased aerodynamic performance and durability. Up to now, fully resolving the turbulence and unsteady flow field through Direct Numerical Simulation (DNS) has been prohibitively expensive due to the requirement to resolve the very large range of temporal and spatial scales in the flow. This paradigm is now beginning to change due to the development of massively parallelizable codes in combination with large-scale computing hardware, which is enabling the use of high-order direct simulation of turbulence at engine-scale conditions.
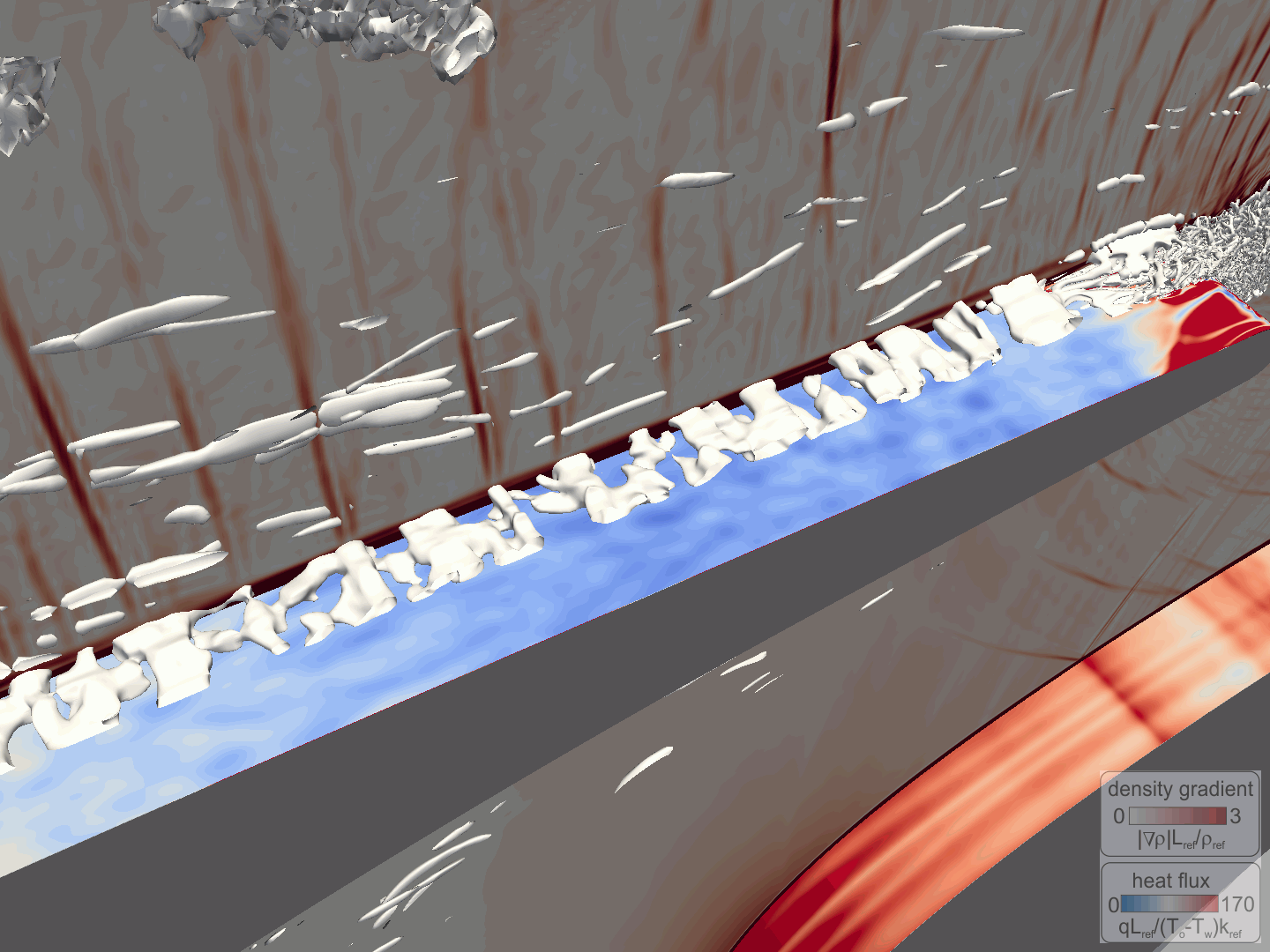
Code development
In order to perform high fidelity simulations we have an in-house high order code (3DNS) which has been specifically developed for turbomachinery flows.
Associated Team