Overview
Transforming heat-recovery system performance by exploiting multi component turbine flows.
Heat recovery systems work by transferring heat into a high-pressure working-fluid, using a heat exchanger. In order to produce electricity, the working fluid drives a turbine which is connected to an electrical generator. Heat recovery systems often use working fluids which are refrigerants or long-chain hydrocarbons. The properties of these working fluids differ greatly from those which have traditionally been used within turbines (such as air within aero-engines/gas-turbines or water vapour within steam turbines) and can be made up of several components including mixtures of gases and liquids. There is very little known about the behaviour of these unconventional working fluids within turbines largely due to a lack of experimental data with which to test current theories. This is important because turbine designers require accurate models in order to develop high performance machines, and uncertainties in the modelling can have a detrimental impact on both the development costs and the overall performance of a heat recovery system. There is also a potential to exploit the unusual behaviour of these working fluids, such as their ability to change from liquid to gas across the turbine, which can be exploited to increase system power to size ratios (power density) in ways not possible using normal working fluids like water.
The work is currently focussed on turbines used within Organic Rankine Cycles which are commonly used for heat recovery. We are performing experiments using a newly developed transient test facility and computational techniques to model these flows. The project is funded by the EPSRC (EP/L027437/1).
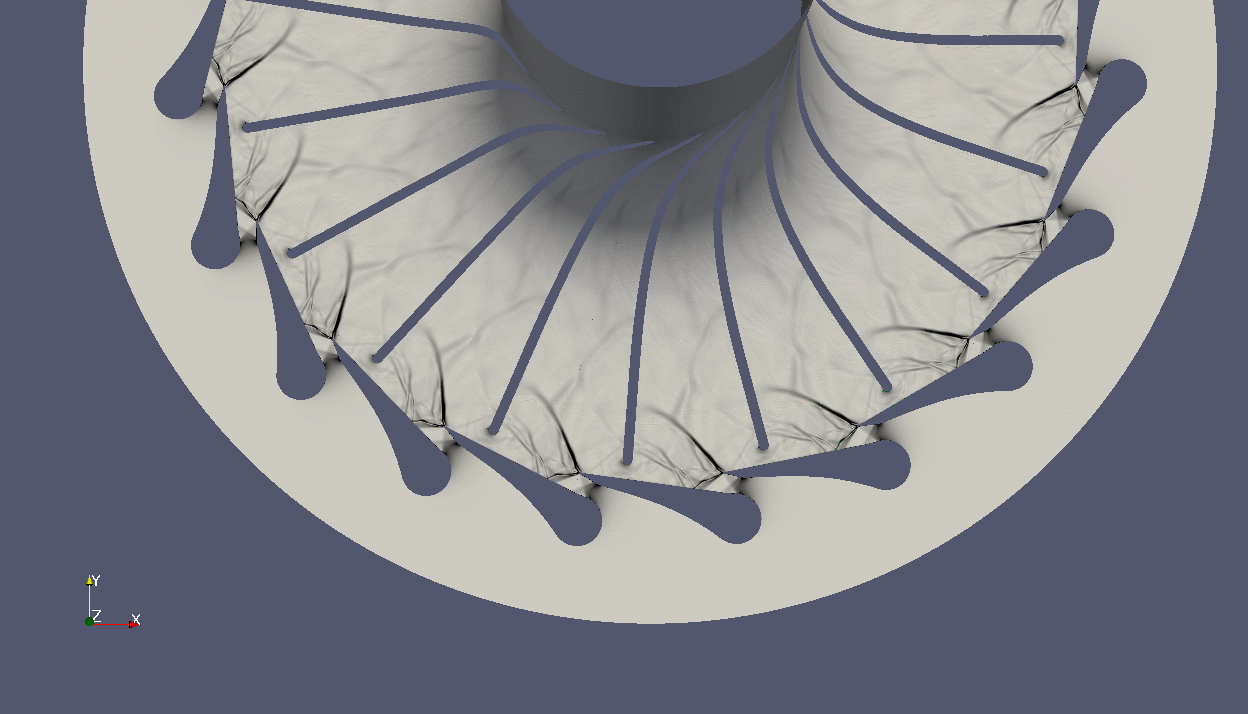
Associated Team